In a previous column, I wrote about the critical necessity to perform destructive testing of welds prior to welding on any vehicle---and regardless of whether your shop is being paid for that procedure.
But I also believe you should be paid for this crucial work, and that’s what I hope to address here.
Those of you who have read my articles in the past on better negotiating know I believe the process involves four questions: Is the procedure necessary? Is it included in any other labor operation? Are there pre-determined times? If not, what it is worth?
Looking at any of the OEM repair procedures should convince you that it is necessary. Here is some of the wording I’ve seen:
BMW: “To determine the optimum electrode contact force for spot-welding, carry our spot-weld shear tests on sample sheet metal.”
Ford: “Place the welded sample in a vice and carry out destructive weld tests by peeling the scrap metal apart using large lock-type pliers. Measure the weld nugget to determine the nugget meets Ford weld nugget requirements.”
Hyundai/Kia: “Test welding must be performed before welding vehicle body.”
Toyota: “Welding strength must be validated by tuning the welder and performing destructive testing.”
I could go on and on, but you get the idea: It is a necessary procedure.
The next negotiation question: Is it included in any other labor operation? No matter which estimating system you are using, you should be able to find that the user’s guide---often referred to as “procedure pages”---lists set-up and performing test welds as a not-included operation.
If you can’t find it, visit the Database Enhancement Gateway and read the estimating system providers' responses to inquiries about this, including #15358 (Solera/Audatex), #12565 (Motor/CCC) and #16652 (Mitchell).
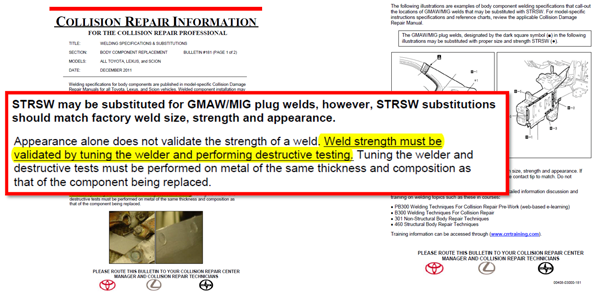
None of the estimating systems publish a labor time for destructive testing of welds, so the answer to the third negotiation question is no.
That leaves you with the fourth question: What is it worth?
I can’t answer that question for you. Perhaps you could conduct your own time study. In any case, remember it should be based on how long it takes an average technician---one with five to seven years of experience---to gather the tools, equipment and supplies needed, perform the task safely, and return the tools, equipment and supplies to their store area, and clean the work area.
Remember, too, material costs for this process are not included. That can include OEM-approved wire, welding tips/nozzles, shielding gas and gun liner. If you’re buying welding coupons, keep that cost in mind.
You can also improve your chances of being paid for this necessary step by documenting the process. Shoot images of the test welds prior to testing, while the test welds are in the vise, and after they destructively tested. If you use an electronic quality control app, you can set it up to require these photos, ensuring they are time- and date-stamped. Some shops also actually label and store the test welds to help limit their liability should any questions about the repair arise down the road.
Remember the automakers state the welding coupons you use should be of the same material with the same coating that the new replacement panel will be attached to. In some cases this may require multiple different coupon thicknesses and coatings, such as galvanized.
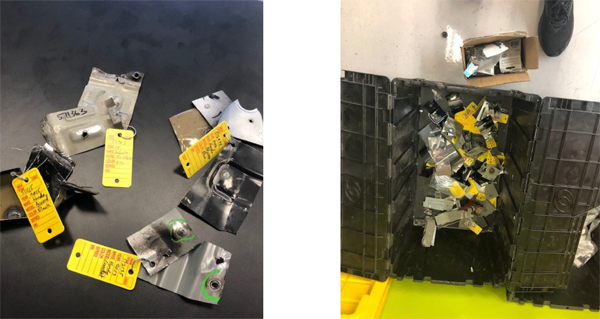
That’s a common oversight, according to Rick Miller of Wadsworth International and a program consultant for Jaguar Land Rover North America and Subaru of America.
Others mistake he sees: Not checking to ensure the correct wire type is in the machine, not understanding what makes a good quality weld, not following the specific placement of welds called for by the automaker, or the use of MIG welding because of a perception that it’s easier than squeeze-type resistance welding.
Potential sources of coupons include I-CAR, your welder manufacturer or Custom Metal Shearing in Ohio.
Some other resources that may be helpful:
CollisionHub offers a welding validation series and will build customer QR series for shops to put on their welding equipment to offer “just in time” training for the tech.
SCRS has some great information on its website, including video of a panel discussion on OEM expectations about welding.
American Honda offers two-day hands-on welding training for anyone in the industry, with a discount for Honda and Acura certified shops. Attendees will learn how to identify steel strengths and thicknesses on Honda vehicles, and how to find Honda service information requirements for each type of recommended attachment method. After completing 13 unique practice joints, attendees are expected to complete multiple replacement procedures.
To register, visit academy.verifactsauto.com, or for questions, email collisioinrepairtraining@na.honda.com.
“Anyone may enroll, but I would suggest this is not a class for beginning welders,” said Scott Kaboos, national assistant manager for collision repair training and technology for American Honda. “It is an advanced level class, and so far we have had a 50% pass rate, mostly because some attendees did not have prior basic training.”
Listen, I mean this in love, but we as an industry need to get it together! We must follow the OEM procedures. Not setting up and performing destructive weld test is not negotiable.
All of the steps above should help your shop join those being paid regularly for performing destructive testing of welds. But whether or not you choose to pursue being paid for it, I can’t stress enough that you need to ensure your technicians are absolutely performing this crucial step every time they will be welding on a vehicle.
Mike Anderson