“If you have a conventional shop environment, where they’re following OEM information to the letter on every repair, only about 30% to 40% of the vehicles they’re repairing will have alignments at the end,” he said. “So, an additional 20% to 30% of vehicles come through, and using the Hunter aligner, we’ve been able to identify suspension misalignment on impacts that largely, as an industry, go unidentified.”
Bradshaw reported alignment checks fail “62% to 68% of the time in any given month.”
“So, using the Hunter aligner has been a major profit center for us,” he said.
On top of that, K & M Collision does a lot of ADAS in-house.
“Many of these manufacturers require suspension alignment to be within factory specifications before performing ADAS calibrations,” Bradshaw said.
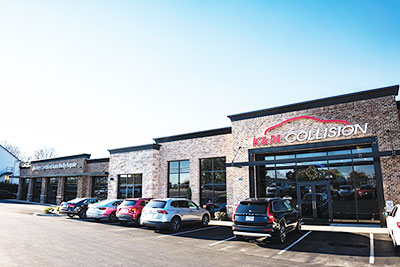
The Hunter aligner has also helped K & M Collision identify suspension misalignments in vehicles whose wheels appear unscathed.
“These are accidents, where the impact is from a direct front or rear hit,” Bradshaw said. “And based on what the industry typically looks at, they’re not considering suspension alignment issues on those cars.”
However, Bradshaw said the pre-alignment check tells a different story.
“Even in these situations, we find misalignments outside the tolerance,” he explained. “And regarding driver safety, the vehicle manufacturers require a steering angle sensor initialization or zero-point calibration after the battery’s disconnected and reconnected. If you’ve got a shop that assumed the suspension alignment is within specification, that can create some issues in the future.”
Based on the impact and manufacturer requirements, K & M Collision uses Hunter’s Road Force® Elite diagnostic wheel balancing machine to check each tire and wheel assembly. A collision repair technician then uses the TCA34S tire changer for tire replacements when needed.
Regarding support from Hunter Engineering, Bradshaw said K & M Collision has had a “very positive” experience.
“The sales rep we have---David---has been accommodating,” Bradshaw said. “When I’m interested in new equipment or have questions, he’s here within a day or two. He also sometimes brings in new equipment for us to demo.”
Bradshaw deals with Todd on the service side, who has a schedule to meet K & M Collision’s needs proactively.
“I can’t think of many times we’ve called Todd, and he hasn’t answered his phone,” Bradshaw recalled. “And when he isn’t available, he always gets back to us immediately.”
Hunter Engineering Co.
314-716-0469
tmaitz@hunter.com
Facebook: @hunterengineeringcompany
Instagram: @hunterengineering
LinkedIn: @hunter-engineering
YouTube: @HunterEngCo
To read more auto body shop profiles from the June 2023 Shop and Product Showcase, click here.
Abby Andrews