“It’s basically driving a computer on wheels,” Chad said. “Now it’s about writing proper estimates, getting repair procedures, documenting everything. Fixing cars properly is more of a challenge.”
With that in mind, the Woodmans are keeping an eye on the future---of both the collision repair industry and the planet as a whole.
In addition to recycling all plastic bumper parts and sheet metal components and taking steps to make its equipment more energy efficient, the shop uses a downdraft spray booth and HVLP (high volume, low pressure) guns, to reduce overspray, which reduces harmful emissions.
Woodman Collision Center also started using a waterborne paint system in 2008, becoming one of the first collision repair centers in the St. Louis area to make the switch.
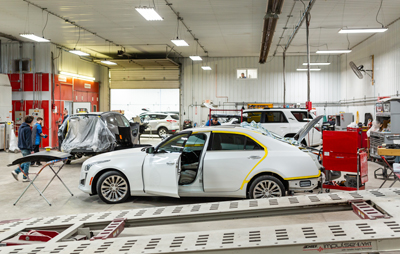
“We’re doing our part to keep the planet good for the next generation,” Ryan said. “It’s also what most OEs are using now, so it just made sense to switch.
“It seemed like that was the forward progress of the collision industry, and we wanted to make sure we were ahead of that.”
The shop website explains that, since it mixes an average of 2 gallons of basecoat per week, the move to waterborne from a solvent system saves more than 600 pounds of volatile organic compounds (VOC) every year---the equivalent of eliminating the emissions of more than 200 cars per year.
In November 2020, the shop tried Axalta’s Cromax® EZ, a waterborne system designed to achieve quality goals with products that provide quick and accurate application, and color tools that are convenient and reliable.
After the initial test run, the shop made the switch to the waterborne system.
“The thing I liked about Cromax was it was user-friendly once you got it into the booth,” Ryan said. “You could sand out any issues you found in the booth.”
The clear coats are more buffable, and the blends easier to lay down. The color match is also top-notch, with a wide range of variants to choose from, and the camera works well to provide a “third eye” when a painter is torn between two variants.
“Those were the big points that led us to switch,” Ryan said. “Our painters like it too for those reasons.
“We don’t have a lot of re-dos because we try to handle that before it gets to the booth, but at times it does happen,” he explained. “Usually it’s just a quick scuff and throw it back in there.”
The shop has multiple Axalta reps it can call for assistance.
“There are two [reps] from the area we have known for a really long time, and they’re on their game and ready if we have an issue,” Ryan said. “They get on it real quick and get it solved.”
Axalta Coating Systems
Company Contact: Heidi Stilwell
heidi.stilwell@axaltacs.com
(610) 358-5353
www.axaltacs.com
Facebook: @AxaltaNArefinish
Instagram: @axaltarefinish
Twitter: @axalta
LinkedIn: @axalta
YouTube: @axalta
To read more auto body shop profiles from the October 2022 Shop and Product Showcase, click here.
Abby Andrews