In 2015, entering into an agreement with PPG was an easy decision. “I used PPG previously, and it was such a good experience,” Shirley said. “My two painters love the product, and they were also familiar with its characteristics and were very comfortable here with the system.”
When it comes to any vendor, Shirley looks for “products, processes and people,” and hit the trifecta with PPG and his jobber, English Colour. At a shop where they have to produce 15 or more vehicles daily, JDS Collision Repair has no leeway for comebacks or anything that can hamper the process.
The shop’s approach is to “pull cars, rather than push” through its production system, and it evidently works. Shirley devised a parts rack system and designated a specific area to disassemble cars and track parts, so they have them ready for each tech when the times come to install them.
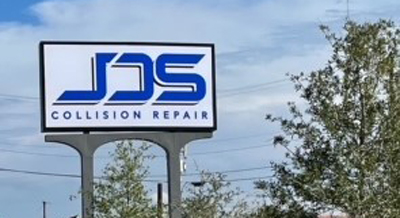
“That way, the tech knows where every part is and we don’t have to run around trying to complete a repair,” he said. “I learned from experience that searching around for parts or waiting for parts is the No. 1 way to mess up your cycle time. We have to keep moving here, so designing these racks and coming up with this system is perfect for us.”
By using the ENVIROBASE® High Performance waterborne paint line on every vehicle, the crew at JDS Collision Center is exceeding everyone’s expectations.
“We hear back from our employees, our insurance partners and, of course, from our customers, and all we hear are compliments,” Shirley said. “We have reduced our booth time considerably and getting more throughput than we ever anticipated. We can’t fall down with this product because I tell people it comes with training wheels. My guys are hitting color matches dead-on, so we never get comebacks, which is a major deal. In addition, we are saving time on curing the vehicles, so it’s been wonderful.”
To educate himself, Shirley and his son have taken classes through PPG’s MVP Business Solutions program.
“I’ve taken production classes, estimating classes and classes about paint processes, and they have all been very valuable. My son has worked his way up the ranks from washing cars for two years to parts and now as an estimator, so the PPG classes have helped him as well."
Tapping into the advantages of working with PPG has helped Shirley on multiple levels, so he is more than delighted to share the news.
“We are happy, what more can we say? You get a product that works, and it’s supported well from both the jobber and the manufacturer, what more can you ask for?”
PPG
Company Contact: Cathy Rusnak
(440) 572-2800
rusnak@ppg.com
www.ppgrefinish.com
Facebook: @PPGRefinish
Instagram: @ppgrefinish
Twitter: @PPGRefinish_NA
YouTube: PPG Refinish (USA/Canada)
To read more auto body shop profiles from the October 2022 Shop and Product Showcase, click here.
Abby Andrews